How are seamless steel pipes produced?
2014-11-21
According to different production methods, it can be divided into hot-rolled pipes, cold-rolled pipes, cold-drawn pipes, extruded pipes, etc. 1.1 Hot-rolled seamless pipes are generally produced on automatic pipe rolling units. The solid pipe blank is inspected and surface defects are removed, cut to the required length, centered on the end face of the pipe blank at the perforation end, and then sent to the heating furnace for heating before being perforated on the perforating machine. During perforation, it continuously rotates and advances; under the action of rollers and a mandrel, a cavity gradually forms inside the pipe blank, called a mother tube. It is then sent to an automatic pipe rolling machine for further rolling. Finally, it is equalized in wall thickness by an equalizing machine and sized by a sizing machine to meet specification requirements. Using continuous pipe rolling units to produce hot-rolled seamless steel pipes is a more advanced method.
1.2 If smaller dimensions and better quality seamless pipes are desired, cold rolling or cold drawing or a combination of both methods must be used. Cold rolling is usually carried out on two-roll mills where steel pipes are rolled in an annular hole formed by variable cross-section round hole grooves and stationary conical mandrels. Cold drawing typically occurs on single-chain or double-chain cold drawing machines with capacities ranging from 0.5 to 100 tons.
1.3 The extrusion method involves placing heated pipe blanks inside a closed extrusion cylinder where a piercing rod moves together with an extrusion rod to extrude the material through smaller die holes. This method can produce steel pipes with smaller diameters.
Previous
Shenyang Tengfei Iron Corporation
Shenyang Tengfei Steel Pipe Co., Ltd.
Address: No.6 A 3, No.13 Road, Economic and Technological Development Zone, Shenyang City, Liaoning Province
E-mail:tfwelcome@163.com
Focus on us
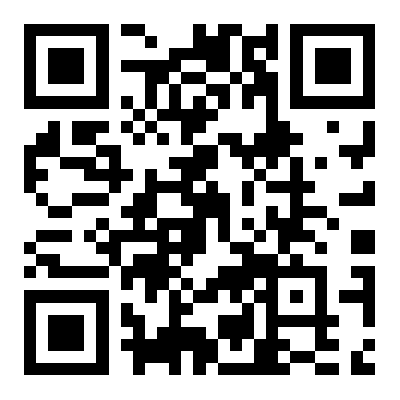
COOKIES
Our website uses cookies and similar technologies to personalize the advertising shown to you and to help you get the best experience on our website. For more information, see our Privacy & Cookie Policy
COOKIES
Our website uses cookies and similar technologies to personalize the advertising shown to you and to help you get the best experience on our website. For more information, see our Privacy & Cookie Policy
These cookies are necessary for basic functions such as payment. Standard cookies cannot be turned off and do not store any of your information.
These cookies collect information, such as how many people are using our site or which pages are popular, to help us improve the customer experience. Turning these cookies off will mean we can't collect information to improve your experience.
These cookies enable the website to provide enhanced functionality and personalization. They may be set by us or by third-party providers whose services we have added to our pages. If you do not allow these cookies, some or all of these services may not function properly.
These cookies help us understand what you are interested in so that we can show you relevant advertising on other websites. Turning these cookies off will mean we are unable to show you any personalized advertising.